Services
We have partnered with the top local & international manufacturing facilities to design process systems according to client specifications & to ensure compliance with local & international standards.
Do you require urgent technical assistance?
We’re available 24/7 for your technical emergencies.
Get in touch witth our technical teams on standby & let our team assist you in getting your facility back online.
GAUTENG, NORTH WEST, LIMPOPO, FREE STATE & EXPORTS
Tel: +27 (0)10 442 5798
Email: gareth@pcsza.com
1 Derek Coetzee, Jet Park,
Boksburg, 1459
KWA-ZULU NATAL
Tel: +27 (0)31 902 1220
Email: chris@pcsza.com
Unit 2, No. 3 Kyalami Road
Westmead, Pinetown
We manage the integrity of our clients’ process equipment portfolio providing long term sustainability & plant reliability.
PCS offers you an array of professionally executed services that accompany our wide range of product offerings. Our valve division is focused on dedicated services supporting all aspects of valve maintenance for the process industry.
CLIENT FOCUSED SERVICES FROM PCS
Our field service contracts cover a full range of activities performed at the highest quality level. From on-call day by day technical field dispatching to longer term contracts, we jointly agree scope and duration.
All work is completed in accordance with health & safety requirements, where safety is our main priority.
Below are a number of different ways in which our agreements can be configured and utilised.
The agreement generates:
- Daily inspection work orders that dispatchers schedule through the schedule board or schedule assistant.
- Monthly maintenance work orders that are automatically scheduled by resource scheduling optimization.
- Weekly work orders where the agreement assigns the same resource each time at a defined start time.
- A single work order each month to inspect multiple customer assets at a customer location.
- Multiple work orders each year to inspect multiple assets at a customer location.
- Quarterly invoices to bill customers for predefined products and services.
Contact our technical sales team for more information.
Our support team furthermore offers your the option of a full maintenance agreement, tailored to suit your requirements.
Agreements can include monthly maintenance of your equipment and a majority of non-wearable parts (subject to abuse).
Our goal is to keep your facilities running effiently and to prolong the lifespan of your plant.
Monthly integrity checks allow for out technicians to identify and fix problems before they cause your loss of production and downtime.
If you’re looking for ways to deliver the technical skills your team requires in your operational environment, reach out to us and let’s discusss the training opportunties that we have on offer for your team.
Let us train your team in the technical aspects of our products, enabling them to become better at what they do for your business.
Improve the availability of spares and reduce your inventry costs through our inventory management service.
We provide you with recommendations for maintaining optimum spare parts stocks and prevent excess stocks or shortages of required spares.
Let our team assist you in identifying which spares your may require within your inventory to keep your facilities up and running, minimising any downtime.
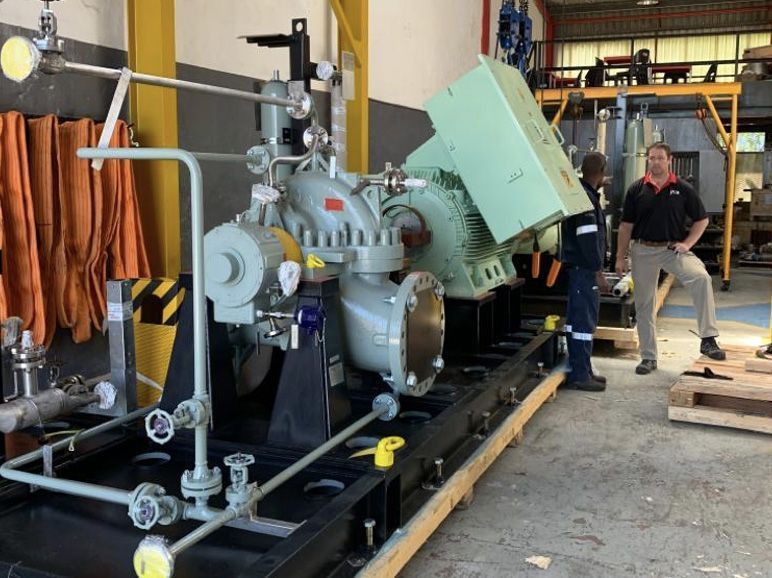
Pump Repairs
Our facilities work ISO 9001/2015 and have full traceability on workmanship & parts. All equipment is tested prior to leaving our facilities.
Seal Repairs
Our mechanical seal repair centers will inspect, report, recondition and rebuild your mechanical seal to “as new” condition. Repairing your seal will reduce cost of ownership while keeping the same life of your rotating equipment. Seals are tested to API 682 (American Petroleum Industry) standards.
Gearbox Repairs
We pride ourselves in being able to repair all types of rotating equipment including gearboxes up to 5 ton. Our expert technical staff repair or replace all wearing components to ensure the best quality product at the best possible price.
VALVE REPAIR
PCS, with our partners, offer repair & testing services for all types of valves which includes API hydrostatic & pneumatic valve leak testing.
PCS has execllent links to major valve manufacturers, we monitor delivery times & technical innovation enabling our customers to recieve valves in a timely manner that meet your technical requirements & costs efficiencies.
Premier Valves
PCS in partnership with valve specialist’s have the capability to design and develop valves in accordance with recognised worldwide standards – API, ASME, ASTM, EN, NACE, ISO, BSI, MSS & PED.
Valve Scope
Mechanical &, on-off & control types. Specifications such as ball, globe, butterfly, gate, diaphragm, desuperheaters, safety valves & more. We also provide replacement parts for renowned international control valve brands.
Refurbishment
PCS is fully equipped to refurbish most makes, types and sizes up to 3 meters of low, medium and high pressure valves. Our facilities consists of stripping, sandblasting, machining, welding, assembly, testing and spraying services.
PCS
Require Technical Assistance?
Get in touch with us 24/7